
An image taken from the team’s computer simulation: the resultant mixing of red and blue air when a shock wave, indicated by the sharp change from dark to light, collides with the turbulent air. Image/Ivan Bermejo-Moreno
Every other summer, Stanford University’s Center for Turbulence Research hosts a group of leading researchers from around the world to collaborate and develop new ideas in the study of turbulence.
Despite the majority of attendees being professors and postdoctoral researchers in field, at the most recent even in 2018, Viterbi School of Engineering PhD students Xiangyu Gao and Jonas Buchmeier joined the group with their advisor, aerospace and mechanical engineering Assistant Professor Ivan Bermejo-Moreno.
“I think it’s a good opportunity for our students to see what’s going on at the forefront of turbulence research, develop some interactions, some networking, and see how different groups are working,” Bermejo-Moreno said.
Together with collaborators from the University of Maryland and Stanford University, they dissected certain intricacies of aircraft engine combustion, specifically the high-speed mixing of air and fuel, through computer simulations. The results of their work could be used to improve the understanding and design of future aircraft engines for hypersonic flight, known as scramjets, and increase their efficiency. Their findings were published by Stanford in January.
Most airplane passengers are focused on what’s happening inside the cabin. Their thoughts dwell on concerns with leg and arm room, noisy neighbors, when the food cart will arrive, and the shoddy Wi-Fi connection. But for aircraft flying at hypersonic speeds – greater than 3,000 miles per hour, or five-times the speed of sound – the real action is happening beyond the thin metal walls.
Inside the combustion chamber of scramjet engines, pressurized air mixes very quickly with fuel and is then ignited in a combustion that occurs at supersonic speeds – greater than the speed of sound. The team set out to study how fast they are able to mix together, which would allow combustion to happen sooner.
“In a supersonic combustion engine, you want the mixing to happen as fast as possible so that the combustion will take place before the mixture exits the engine,” Bermejo-Moreno said.
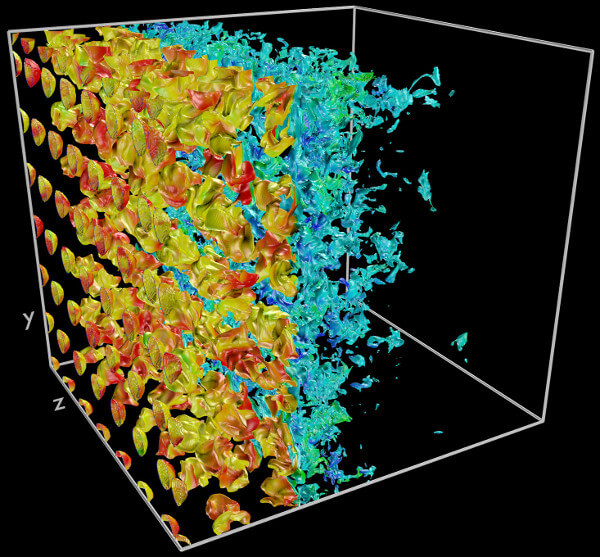
Image taken from the team’s computer simulation: the abrupt change from high speed (red) to low speed (blue) air, indicating the location of the shockwave. Image/Ivan Bermejo-Moreno
The mixture is swirling around at high speeds and causing rapid changes in pressure and flow velocity, motion characterized as turbulent flow. In addition, sudden jumps in pressure, temperature and density, called shockwaves, develop in the chamber. When these shockwaves collide with the turbulent mixture, the turbulence is amplified, making it even more erratic, and the shape of the shockwave is deformed.
This is what they want to happen, as it is critical to the function of a supersonic engine. “Turbulence stretches and rotates the fluids much faster,” says Bermejo-Moreno, enhancing mixing at the molecular level. Their study is among the first to connect the effect of shockwaves on the turbulent mixing of passive elements that don’t affect the properties of the fluid flow, such as velocity, pressure and temperature.
But as you can imagine, creating a computer simulation of this event is not easy. Capturing the high speeds and changes in flow properties requires an immense amount of computational power, beyond what even a supercomputer can do. As such, in addition to concentrating on passive mixing, they developed a highly precise simulation of what are called the “fine scales” of turbulence – dominated by inertia and dissipation.
“With our results, our findings, we can come up with a model of these small scales. And then this model can be very useful in the design of future engines,” said Gao, first author of the study.
In addition to performing a statistical analysis on the system, Gao, majoring in mechanical engineering, is investigating the effects of different physical parameters on mixing. Over the summer he concentrated on the shock and turbulence Mach numbers, which dictate the strength of the shockwave and the fluctuating velocity of the turbulent flow. Now he is investigating how increasing another property related to fluid flow, called Reynolds number, can affect supersonic turbulent mixing.
To track how the system changes during mixing, Buchmeier, an aerospace engineering major, is developing diagnostic tools. Through his algorithms, they are able to characterize the geometry of the turbulence and mixing and look for patterns that can be used in computer models for a better prediction and control of the flow in future scramjet engines.
The month-long summer project was only a small study within larger ones Gao and Buchmeier are currently working on for their doctorate degree. They are now expanding their work and developing new simulations and tools to further their understanding of mixing for the improvement of aircraft engines.
Published on April 3rd, 2019
Last updated on May 16th, 2023