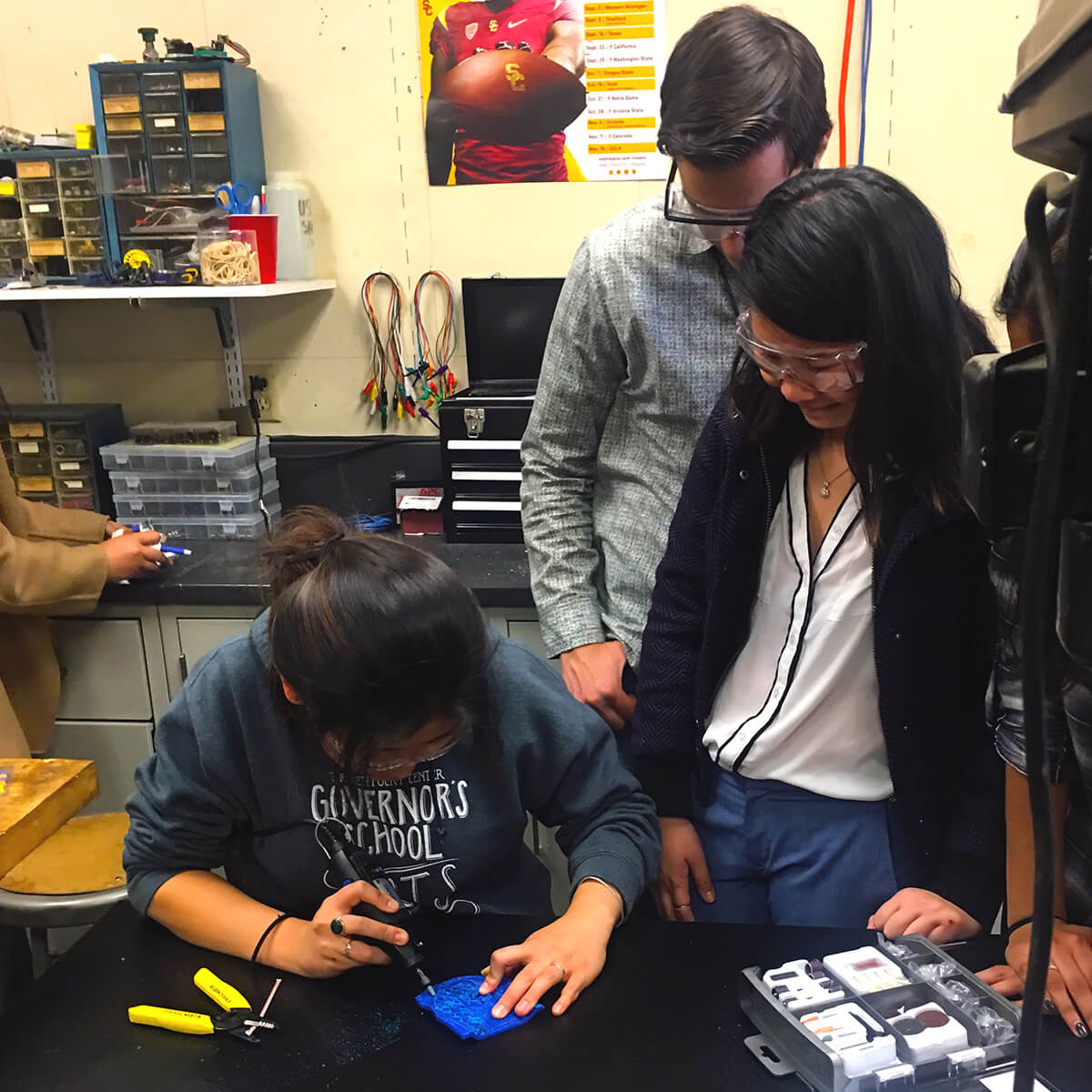
Team Sparkys hard at work in the USC Fabrication
Lab Photo / Tilden Chima
The USC Associated Students of Biomedical Engineering, ASBME, hosted its annual make-a-thon from February 23rd to 25th. Now in its third year, the event, geared towards designers as opposed to coders, saw more than 80 people in teams of four to five tackle medical device designs within a 30-hour period
This year, the design challenge was building an inexpensive, customizable, and accessible prosthetic arm. Other requirements included: a cost ceiling of $250 or less; an extension-based hand grip mechanism; a user grip feedback mechanism; and maintaining a user-friendly design. The challenge was sponsored by the Musculoskeletal Orthopedic Research and Education Foundation, or MORE, a non-profit organization based in Phoenix dedicated to treating musculoskeletal conditions. Helping Hands, an organization that provides free-of-cost prosthetic hands to children with upper extremity deformities, came up with the challenge problem.
To kick off the competition, students gathered at 6 p.m. for the challenge reveal by Ani Nayak, director of biomechanics research at the MORE Foundation. The 18 participating teams were then handed toolkits in preparation for computer-aided design (CAD) design submissions due by 3:30 p.m. the next day.
After the initial design stage, five fabrication teams were selected by the judges to proceed to the prototyping stage, where they would fabricate their designs using the facilities in the USC Fabrication Lab, and 3D printers provided by USC 3D4E, USC’s 3D printing club.
Here are the teams that made it to the prototyping stage:
- The Mightytochondrias (Neta Glaser, Alexander Ramirez, Alana Stein, Margot Mel de Fontenay)
- MEDesign Team 1 (Andrew Yock, Margaret Field, Lacy Schneeman, Seth Krieger)
- Sparkys (LySandra Vuong, Daniel Donchev, Young-Kyung Kim, Priscilla Pan and Tanuja Mohan)
- MEDesign Team 3 (Jason Blair Lewis, Cassandra Argumedo, Robert Sutherland, Ahmed Mohammed)
- The Avengers Assembled (Nina Singh, Myrl Marmarelis, Patrick Mcdonnell, Adithya Bellathur, Dominie Miyasato, Sovanna Cao)
“We thought of Iron Man because kids like superheroes, and we thought that we could implement a sensor that looks like that on Iron Man’s bionic arm,”
Myrl Marmarelis
Myrl Marmarelis and Nina Singh, juniors in computer science and biomedical engineering, respectively, led The Avengers Assembled to build a solution they dubbed “Project Iron Hand.”
“We thought of Iron Man because kids like superheroes, and we thought that we could implement a sensor that looks like that on Iron Man’s bionic arm,” Marmarelis said. “Our idea is unique in that while most solutions are purely mechanical, ours integrates electrical components.”
Added Singh: “We are including sensors to help the kids switch between extension and flexion modes and vibration sensors to give real time feedback on grip strength.”
The Avengers Assembled clinched the Most Innovative Award for demonstrating exceptional product development and design skills.
However, the team to supersede them all and emerge as the winners of the competition was MEDesign Team 1 led by Andrew Yock and Margaret Field, an underclassmen duo majoring in biomedical engineering and mechanical engineering, respectively, who have a history of competing at, and winning, medical device hackathons.
Yock said that their main goal was to maintain the full functionality of the hand while keeping costs low using a wire system through the hand.
“This meant avoiding the use of any electrical components,” Yock said.
Yock and Field inserted two wires above the axis of rotation in the hand that would ultimately be responsible for the extension grip, then two wires below that were responsible for the flexion grip.
“The distance of the wires from the axis of rotation was responsible for the full range of motion,” Yock explained.
The duo also chose a tactile feedback strategy.
“Our system comprised of finger wire lines whose tension was translated into a whipple tree: which is essentially a device that helps distribute force evenly through linkages,” Field said. “We added a spring to the end of the whipple tree that compressed as the tension increased. A peg connected to the spring helped push a rubber stopper into the child’s hand for tactile feedback.”
Jason Blair Lewis, a computational neuroscience and classical guitar major, who led MEDesign Team 3, said that his experience taught him that “creative thinking is sometimes more important than heavy engineering aspects and as long as you can make your design as simple as possible and make it work, then you can have the winning design.”
See the ASBME 2018 Makeathon YouTube Video below
Published on April 5th, 2018
Last updated on April 10th, 2018