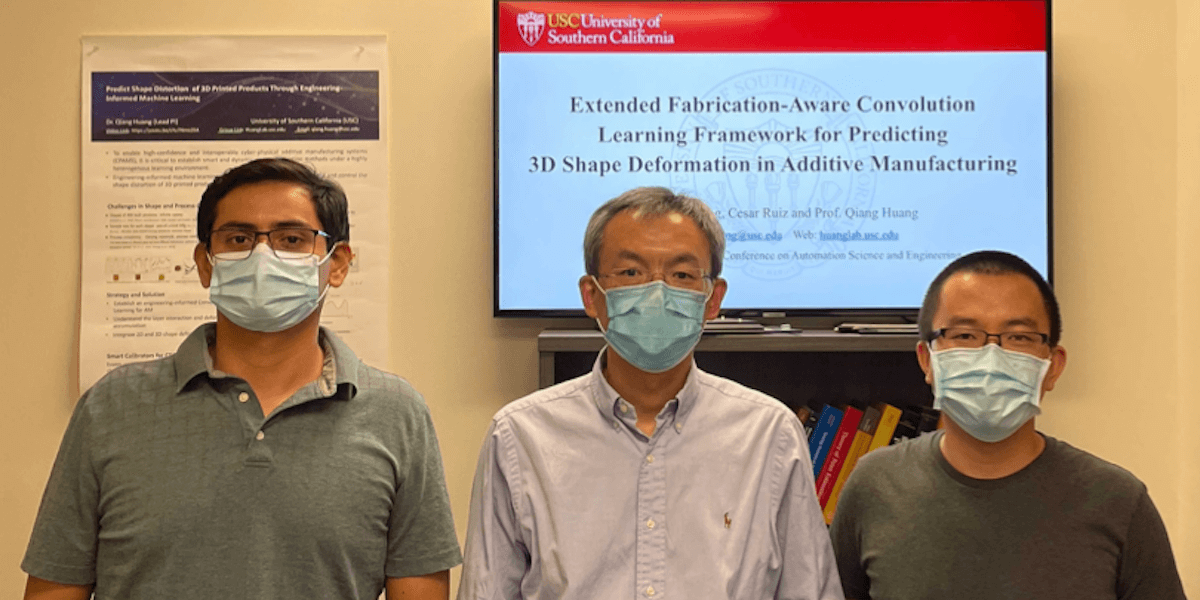
Cesar Ruiz, Qiang Huang and Yuanxiang Wang were awarded the best conference paper at IEEE’s 2021 International Conference on Automation Science and Engineering. Image/Qiang Huang
A new model to vastly improve 3-D printing accuracy was recently honored with the IEEE Best Conference Paper Award at the 17th International Conference on Automation Science and Engineering (CASE), presented by the IEEE Robotics and Automation Society in Lyon, France.
The work was presented by Ph.D. candidate in the Daniel J. Epstein Department of Industrial and Systems Engineering, Yuanxiang Wang, along with postdoctoral researcher Cesar Ruiz and Professor of Industrial and Systems Engineering Qiang Huang.
3-D printing, or additive manufacturing, has been gaining momentum as a novel manufacturing technology that has the potential to revolutionize a range of industries. However, 3-D printing is also subject to printing imperfections. Finished products can deviate from the design for a range of reasons, such as the product’s shape complexity, the print process control and material’s properties. In order to successfully print products, shape prediction models often need to learn from a wide range of shape deviation data.
Wang and his collaborators have now developed a machine learning methodology informed by engineering and based on small sample sized data. The model can learn and predict deviations of smooth and non-smooth 3-D shapes in a unified modeling framework.
“Patterns of shape deviations vary with shape geometries, sizes, materials, and 3-D printing processes,” Wang said. “Due to high customization and manufacturing cost, only a small number of samples are printed, each with very distinct shape deviation pattern. It is extremely challenging to learn and predict geometric quality with a small set of heterogenous shape data.”
Wang said that by learning heterogeneous shape deviation data, the model can establish the association between smooth base shapes and non-smooth shapes.
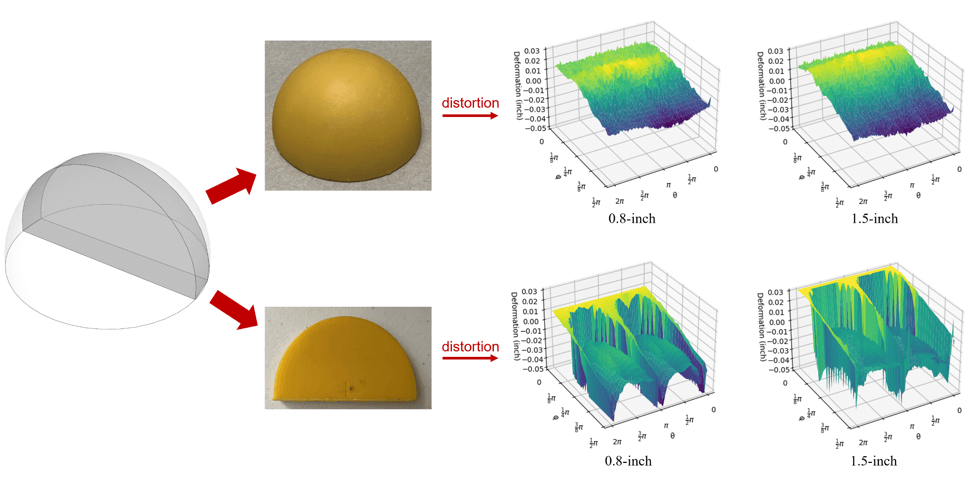
The new machine learning model can draw on data to learn and predict how a printed object’s shape may deviate.
“In essence, we mathematically decompose the additive manufacturing process into two steps: additively fabricating smooth base shapes using a convolution framework to model the layer-to-layer interactions, and then removing extra materials using a cookie-cutter function,” Wang said.
The new machine learning framework provides a new data analytical tool for shape engineering in additive manufacturing and beyond.
“The unified modeling approach we have developed is capable of predicting distortion of various geometries by enabling knowledge transfer from smooth shapes to non-smooth ones,” Wang said. “We are in the process of extending this methodology to 3-D freeform shapes.”
Wang said the new model can be applied to broader engineering domains beyond 3-D printing. Under Huang’s supervision, Wang and his teammates are also developing a software prototype to demonstrate the methodologies for broader impacts. Visit the Huang Lab website for more information.
Published on September 13th, 2021
Last updated on September 13th, 2021