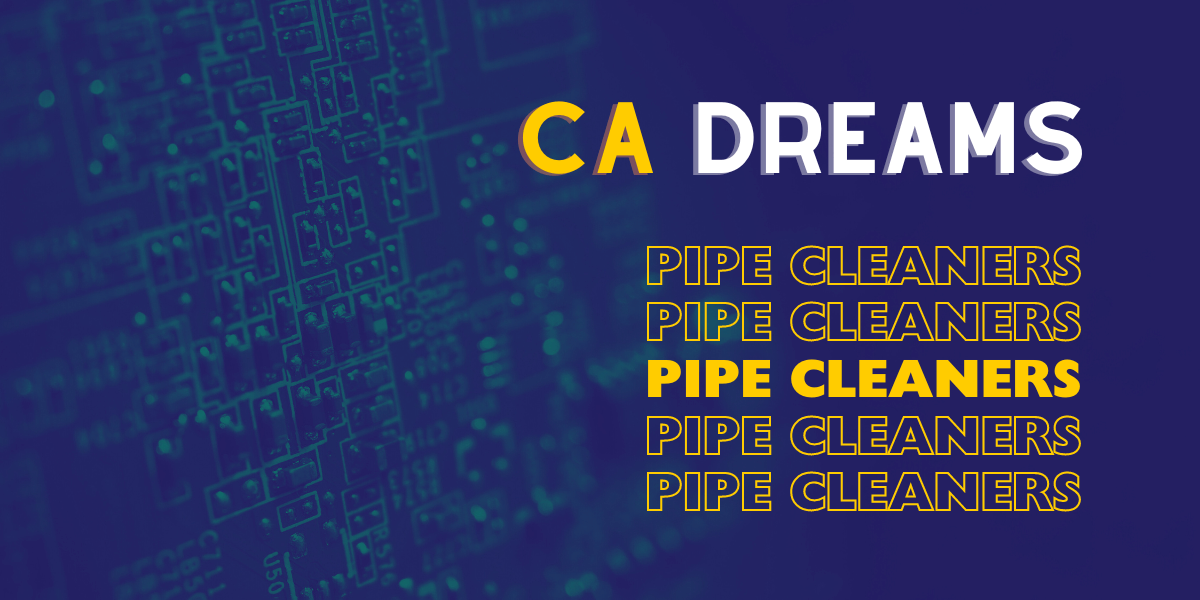
California DREAMS Pipe Cleaners
Precision and repeatability are fundamental to the microchip fabrication process. A single nanoscale error can render thousands of devices useless — a costly mistake.
But because university nanofabs employ the same machines to experiment with a variety of different types of microchips, they have long struggled with process variability and equipment reliability. These issues can significantly slow the transition of innovative designs from research to commercial production.
Enter PDF Solutions, a company headquartered in San Jose, California that specializes in semiconductor big data analytics to provide software solutions that boost output and reliability at every level of the manufacturing process.
The approach allows foundries to identify subtle patterns and anomalies in the machine that might indicate impending issues or explain unexpected results. This could advance the key objective of the California DREAMS hub: speeding up research cycles and improving outcomes.
New tools for academic nanofabs
In efforts to advance the lab-to-fab transition of semiconductor technology, California DREAMS, a regional innovation hub in the Microelectronics Commons led by USC Viterbi’s Information Sciences Institute (ISI), is introducing PDF Solutions’ successful tools into a novel setting: the academic nanofab.
“What we’re trying to do is very different,” said Mike Haney, part of the USC-led program management team. Haney serves as the deputy director of DREAMS and the director of MOSIS 2.0, the hub’s multi-project wafer fabrication service. “We’re using the same tools not to improve chip yields directly but rather to improve process flows. The goal is to see if we can have a similar impact on the nanofab processes that we are developing within our university teams.”
Unlike industrial facilities, university nanofabs handle diverse projects with frequent changes in processes and users, making uniformity and repeatability challenging. The DREAMS hub and MOSIS 2.0 further complicates this issue by uniting multiple universities’ nanofabs—each with its own equipment and processes—into a single, collaborative network.
But implementing PDF Solutions’ data analytics tools and AI approaches could help the DREAMS hub enhance the overall process efficiencies in its university nanofabs. The software helps identify subtle patterns and anomalies in machinery, potentially predicting issues or explaining unexpected results. This could improve development and processing speeds and, critically to the hub, uniformity across partnering facilities.
“If successful, we’ll have the opportunity to accelerate the transition of these processes to our full-flow defense industrial base partners and improve our offerings through MOSIS 2.0,” Haney said.
A unique Hub collaboration
The University of California, Santa Barbara (UCSB), one of the DREAMS hub’s academic partners, is spearheading this innovative approach. Through a collaboration facilitated by the hub, UCSB gained access to PDF Solutions’ software—a resource typically beyond the financial reach of most universities.
“The PDF Solutions project was 100% driven by the Microelectronics Commons,” Demis John, a process scientist manager at UCSB’s NanoFab, said. “We had never heard of this company before we started putting this hub together.”
The partnership has led to the successful implementation of advanced data analytics in a university nanofab environment, providing new insights for process improvement to be used across the hub. It has already yielded two significant findings.
The project focused on improving two types of etching machines in UCSB’s NanoFab: one for silicon dioxide (SiO2) and another for III-V materials, two of the most applicable materials classes for the Microelectronics Commons. Etching, the process of removing material to create intricate patterns on semiconductor wafers, is one of the fundamental steps in chip production.
A common challenge in university labs is the inconsistent behavior of etching machines. Etch rates may vary unexpectedly, resulting in processes that are too fast, too slow, or produce unintended effects. The root causes of these variations are often elusive, making it difficult to predict or prevent such issues, thereby slowing down development.
Big Sensor Data
PDF Solutions’ software helps monitor machine health by analyzing vasts amounts of data collected from sensors on the machines and then comparing that data with the results of the processes those machines are involved in. Semiconductor fabrication tools are equipped with over 100 internal sensors, continuously measuring parameters like chamber pressure, gas flow rates, RF power, and substrate temperature — similar to the sensors on a car.
“Their software basically tells us, ‘Out of these 100 sensors, look at this one. That’s the one that did something different on this run,’” John explains. “It’s using machine learning to analyze a huge amount of data that humans could barely wrap their heads around.” This has helped solve two problems for the UCSB team.
First, when a ceramic clamp in one of the etching tools broke and was replaced, researchers observed a sudden 20% increase in etch rate. At the time, they had no idea this output involved the clamp. But using PDF Solutions’ analytics, they identified a sensor — DC bias voltage — that had an anomalous increase. It happened on the day the new clamp was installed.
“PDF Solutions pointed us to the right sensor,” Brian Thibeault, the Technical and Operational Director at UCSB’s NanoFab, said. “You can see why having all this data very easily and readily available allows us to identify issues right away.”
Second, and perhaps more importantly, the team discovered that their measurement methods, not the machine itself, was the primary source of observed variation in their etch rates. Initially, they recorded a 20% variation in output and assumed that this reflected the tool’s normal performance.
“The story everyone believed was that you can never get a repeatable process out of a university lab,” John said. “Because of our project with PDF Solutions, our plot shows: yes you can.”
This 5% variance rate not only assures that the etch machine is working as expected, but it also suggests that processes developed in the lab show promise for repetition and scaling at the fab level. Thibeault emphasized the practical impact: “Reducing failures saves everyone time and money.”
Improving nanofab processes step-by-step
Going forward, the UCSB NanoFab aspires to connect PDF Solutions software to other fabrication tools, setting up automated machine health recipes that measure and verify the performance of their systems in real-time. This approach could help minimize system downtime, anticipate failures, and predict maintenance. By improving overall machine performance in the university laboratory, researchers can have more confidence that their work can be repeated and scaled in larger industry nanofabs.
“This collaboration’s success provides tangible data that we’re on the right path to accelerating lab-to-fab transitions,” said Damon McCaskill, a senior project manager for the hub. “It’s one of many incremental advances that, collectively, will contribute to the victory of California DREAMS.”
Published on September 22nd, 2024
Last updated on September 23rd, 2024