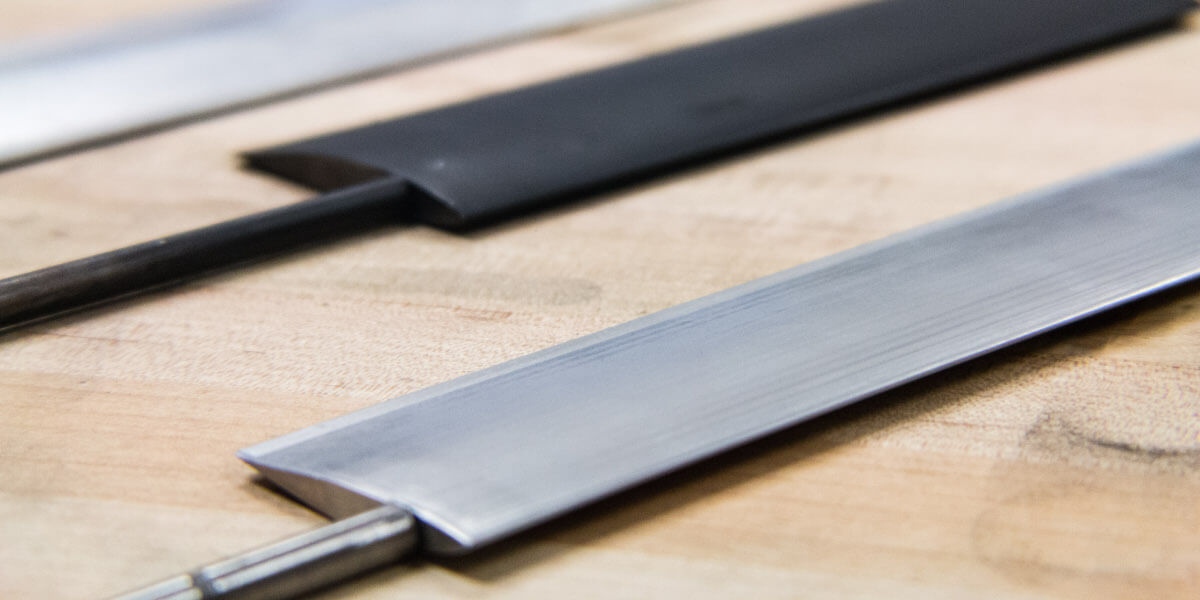
Airfoil designs for testing in the USC Dryden Wind Tunnel. Photo/Valentina Suarez
Since the Wright brothers took to the sky in 1903 aboard their notorious, dual-winged biplane, we have seen countless wing designs of various shapes and sizes used on aircraft.
Each of these wings have a particular cross-section design, known as an airfoil, that follows the textbook standard relationship between lift and the angle of attack. However, Professor Geoff Spedding, of USC Viterbi’s Aerospace and Mechanical Engineering Department, found otherwise while performing careful experiments in the same standard conditions, but at a smaller scale. His results highlight the disparity between experiments, computations and aerodynamic models and how much work still needs to be done before reaching agreement as designers endeavor on small-scale flight – the next generation of drones.

PhD student Joe Tank standing in front of the Dryden Wind Tunnel with the airfoil inside. Photo/Valentina Suarez
“Suppose you’re trying to do a computation. If your computation is right, it should reproduce our findings, and so far, no computations have,” Spedding said. “If you are an aerodesigner and you care about rational design and you want to design an efficient wing, you can’t because you can’t claim to know with reasonable certainty how the wing will behave. In fact, until some agreement is established, neither experiment, nor computations can be regarded as settled.”
The standard says that as the angle of attack increases, which is the angle between the wing and the oncoming air, lift also increases. Put simply, as the aircraft tilts upwards, it generates more lift, making it go higher. This continues until a critical angle, after which the airplane will stall and the lift drops, causing the plane to lose altitude.
However, the airfoil design that Spedding and Ph.D. student Joe Tank (M.S. AE ’14) tested using USC’s Dryden Wind Tunnel had a much different outcome. With a wingspan of just over a foot and a half, a size often used in sail planes and unmanned surveillance aircraft, it fell into a special region that Spedding has a lot of experience in.
“We’ve been finding these curious little known or unknown things in regular fixed wings just because they’re small, but not too small,” he said. “So, it’s the ‘Goldilocks Wing’ – just the right size where the aerodynamics becomes extraordinarily complicated.”
“You can get something that works in these dirty conditions, but you can’t claim that you’re doing design,” said Spedding.
In their tests, instead of lift going up as the angle of attack increased, it dropped. In fact, it went negative, which is something that Spedding says, “never happens.” Then, again to their astonishment, it went way up resulting in a “super-lift” effect before eventually tapering off in a gradual stall.
“When I first processed the data, I thought something was wrong with the test setup,” said Tank. “But after I repeated the test several times and got the same result, I was excited because it was something new and, as far as I knew, it hadn’t been written about before.”
After months of retesting, recalibrating and using new instrumentation and a new airfoil model, they had the same results and the same question: “How is this happening?” The answer turned out to be surprisingly simple, but led to a new, and somewhat tricky, design consideration.
“When a symmetric airfoil is at zero degrees, the flow always goes over it in a nice, symmetric way. But, because this airfoil is a certain size, the flow is always separated before the trailing edge,” explained Spedding. “So, the effective shape of the airfoil is not just the solid body, but the solid body plus this separation region, and it changes as you change the angle of attack.”
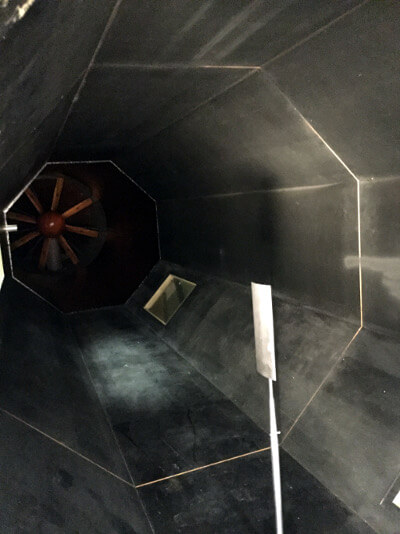
The airfoil inside the Dryden Wind Tunnel. Photo/Joe Tank
Nevertheless, planes with this wing size and design are still able to fly due to the normally unsettled or turbulent conditions they experience.
“You need almost perfect experimental conditions to observe this. Otherwise, there’s so much noise around that shifts these separation points and you can’t make it out from the noise,” he said. “You can get something that works in these dirty conditions, but you can’t claim that you’re doing design. You’re doing a sort of building and testing, building and testing – trial and error.”
As only the second research paper published with these findings – the first a much-overlooked 1983 study using dated techniques but with similar results – Spedding hopes their discovery will inspire other researchers to take a closer look and reexamine their experimental and computational methods. As he puts it, “The question still remains about establishing agreement so that you’re computing and doing experimentation on the same thing. We haven’t done that yet.”
Working with San Diego State University Professor Guus Jacobs, who specializes in computational fluid dynamics, Spedding and his team have already taken the first step. They have only completed the first year of their three-year project funded by the Air Force Office of Scientific Research (AFOSR) and have already found promising (and surprising) results with an airfoil of a slightly different design, but similar size.
“I found this a number of times: as soon as you start looking carefully at something, if you’re willing to take the time, you get surprised. It’s amazing,” said Spedding.
Published on September 19th, 2017
Last updated on February 1st, 2018